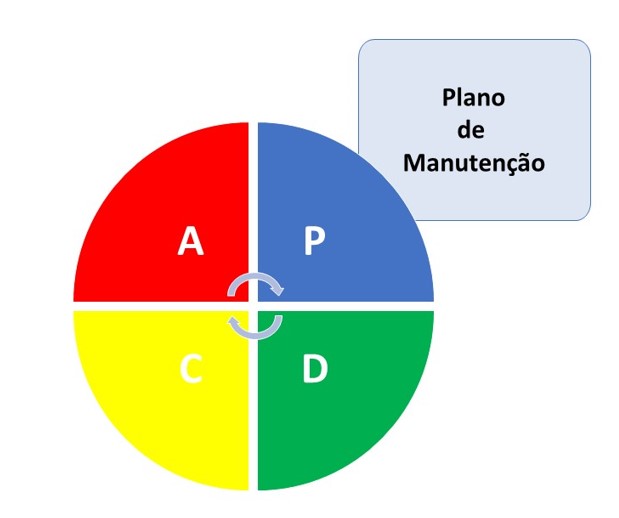
Nesse tópico, o foco do ciclo PDCA é no P – Planejamento e mais especificamente no Plano de Manutenção, que na sua elaboração deve levar em conta vários pontos, tais como:
- Cadastro dos equipamentos;
- CMMS/Árvore de equipamentos;
- Classificação/Criticidade dos equipamentos;
- Conhecimento sobre os equipamentos;
- Como esses equipamentos falham;
- A frequência com que falham (taxa de falha, MTBF, etc.);
- A consequência da falha (segurança, meio ambiente, processo produtivo e o negócio);
- Os recursos disponíveis.
De posse dessas informações é possível definir a estratégia de manutenção a ser adotada, entendendo-se que equipamentos de importâncias diferentes terão estratégias de manutenção diferentes, daí a importância da classificação/criticidade dos equipamentos.
Tratando-se de sistema elétrico, por exemplo, para que se tenha energia na carga é necessário que todo o circuito a montante esteja operacional, ou seja, disponível e confiável, reforçando a máxima: “uma corrente é tão forte quanto o seu elo mais fraco”.
Idealmente para a elaboração e implantação de planos de manutenção deve-se basear nos princípios gerais estabelecidos no Pilar de Manutenção Planejada do TPM – Total Produtive Maintenance, com a utilização seletiva da metodologia do RCM – Reliability Centered Maintenance, e aplicando-se FMEA – Failure Mode and Effect Analysis.
Essa metodologia exige a criação de um projeto, a formação de uma equipe de trabalho dedicada, com cronograma estabelecido o que consome tempo e tem um certo custo. Uma alternativa bastante utilizada é aplicar parcialmente a metodologia do TPM/RCM/FMEA, tomando-se por base:
- Os dados coletados da planta;
- A documentação dos fabricantes;
- As exigências da legislação;
- As normas técnicas;
- A literatura de confiabilidade (banco de dados de modos e taxas de falha da ABRAMAN, OREDA, RAC, IEEE std 500, AIChE, etc.);
- As boas práticas de manutenção e experiências anteriores.
Então, para que sejam definidas para cada família de equipamento, as tarefas de manutenção (O que fazer), as frequências das intervenções (Quando) e as tecnologias a serem empregadas (Como), faz-se necessário um aprofundamento dos tópicos listados anteriormente, o que é tratado subsequentemente.
Cadastro de Equipamentos
Para elaboração do plano de manutenção deve ser considerado um Cadastro de Equipamentos fidedigno, ou seja, um inventário dos equipamentos do sistema em foco, relacionando as identificações (TAGs, KKSs, etc.), as localizações físicas e no processo, as características (dados de placa), etc.. O cadastro será fundamental para a implementação no CMMS da Árvore de Equipamentos.
Esse inventário possibilita a identificação das Famílias de Equipamentos que compõem a planta industrial e assim proporciona facilidades nas definições do Plano de Manutenção.
Entende-se como Família de Equipamentos, equipamentos com características similares, que geralmente têm processos de falha semelhantes, então que podem compartilhar as mesmas estratégias de manutenção. Exemplo de Família de Equipamentos:
- Motor de Indução de BT;
- Motor de Indução de MT;
- Bomba Centrífuga Horizontal;
- Ventilador Axial;
- Etc.
Processos de Falha
Os equipamentos de um modo geral são submetidos a diversos tipos de solicitações, sendo alguns equipamentos mais susceptíveis a determinados estresses do que outros, o que provocam falhas ao longo dos seus ciclos de vida. Em geral, essas solicitações são:
- Térmicas
- Envelhecimento térmico – a perda das propriedades dos materiais ou componentes devido aos efeitos térmicos, próprios da operação normal do equipamento, ou anormais por outras influências externas, por exemplo;
- Sobrecarga térmica – a operação em condições diferentes das quais o equipamento foi projetado;
- Ciclo de carga – o regime de aquecimento e resfriamento em função da variação de demanda;
- Elétricas
- Envelhecimento da isolação – a perda normal das propriedades dielétricas dos materiais isolantes que deve ocorrer no final da vida útil esperada do equipamento;
- Transiente de tensão e corrente – os surtos de tensão e/ou correntes de altos valores (curtos-circuitos) que atingem o equipamento;
- Descargas parciais (corona) – as pequenas descargas elétricas envolvendo a isolação causam danos aos materiais isolantes e consequente podem levar a falhas;
- Mecânicas
- Vibrações – vibrações do próprio equipamento, ou de equipamentos ou instalações vizinhas;
- Choque mecânicos – causados ao equipamento durante o transporte, montagem, manutenção ou operação;
- Outros Esforços (tração, compressão) – ocorridos no processo de montagem, manutenção ou operação;
- Químicas
- Corrosão galvânica – nas conexões com materiais diferentes ou devido a própria atmosfera local;
- Ataque químico – do ambiente onde está instalado ou do uso de produtos;
- Ambientais
- Intempéries – umidade, chuva, vento, calor do sol, salinidade, etc., que atacam o equipamento;
- Poluição – poluentes (pós, poeiras, gases, óleos, graxas, etc.) que se depositam sobre os equipamentos causando dificuldades de troca térmica, entre outros problemas, impedindo o funcionamento adequado dos componentes.
- Biológicas
- Fauna – presença de animais e/ou insetos que podem causar obstrução do sistema de ventilação ou curtos-circuitos;
- Flora – presença de plantas (arbustos, trepadeiras, etc.) que podem criar caminhos para descargas elétricas e até provocar curtos-circuitos.
Com base no exposto acima e objetivando identificar esses processos de falha ainda em fase inicial, várias tecnologias manutenção estão disponíveis e que aplicadas individualmente ou de forma associadas, são ferramentas de grande valor para a manutenção dos equipamentos elétricos, o que será tratado no próximo tópico.
📚 Glossário 📘
ABRAMAN – Associação Brasileira de Manutenção;
AIChE – American Institute of Chemical Engineers;
BT – Baixa Tensão;
FMEA – Failure Mode and Effect Analysis;
IEEE – Institute of Electrical and Electronic Engineers;
KKS – Sistema de identificação de equipamentos alemão (Kraftwerk KennzeichnenSystem) muito usado em usinas térmicas;
MT – Média Tensão;
OREDA – Offshore and Onshore Reliability Data;
RAC – Reliability Analysis Center;
RCM – Reliability Centered Maintenance;
TAG – Sistema de identificação de equipamentos;
TPM – Total Produtive Maintenance;