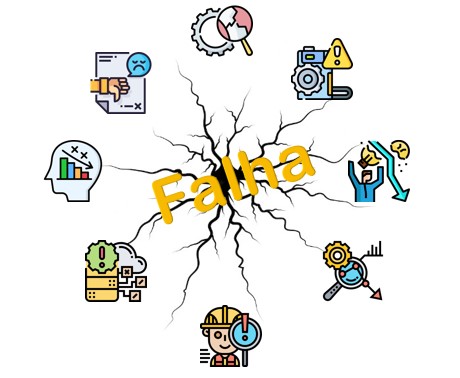
Já tratamos sobre Modos de Falha e a Importância das Estatísticas de Falha (ver esses artigos no link http://elektreng.com.br/category/papo-tecnico/), então vamos um pouco mais a fundo nesse tipo de evento indesejado, que é a falha, mas que deve ser bem conhecido para que se possa evitá-lo ou mitigar os seus efeitos.
- Falha
Como já definido no artigo anterior “Falhas & Modos de Falha”, conforme a ABNT NBR 5462-1994, Falha é: Término da capacidade de um item desempenhar a função requerida.
A caracterização do processo que envolve uma falha é ilustrada pela figura a seguir e detalhada pelos conceitos subsequentes.
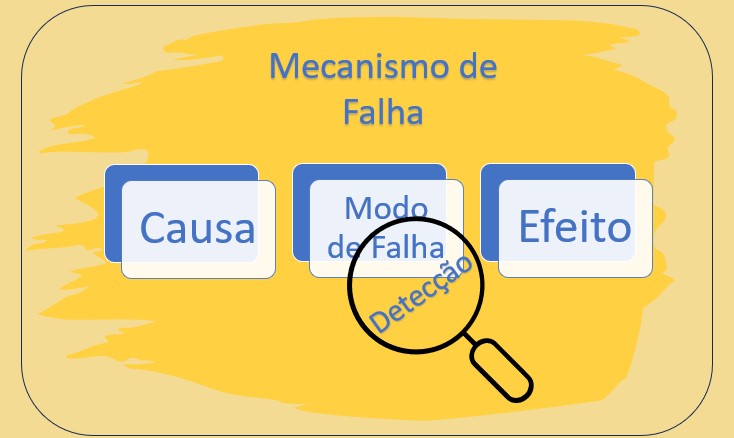
Então, destaca-se dessa ilustração:
- Modo de Falha
É a forma ou meio como uma falha de um sistema, equipamento ou componente se apresenta. Para mais detalhes ver a postagem anterior “Falhas & Modos de Falha”.
- Causa da Falha
Segundo a ABNT NBR 5462-1994: são as circunstâncias relativas ao projeto, fabricação ou uso que conduzem a uma falha.
Por outro lado, a ISO 14224-2016 define como sendo: as circunstâncias que levam a falha.
As duas normas têm conceitos semelhantes.
A causa da falha pode se originar durante a especificação, o projeto, a fabricação a instalação, a operação ou na manutenção de um item.
A Causa da Falha, pode ser subdividida em:
- Causa Imediata
Aquela que resulta na forma com que a falha se apresenta, ou seja, é quem produz o Modo de Falha. O vazamento do fluído numa bomba se apresentar como a Causa Imediata, não sendo a causa raiz da falha.
- Causa Contribuinte
É uma causa que sozinha não é suficiente para produzir ao evento de falha, mas que contribui de alguma forma a produzir a falha.
Uma causa contribuinte pode influenciar os eventos de falha de forma indireta, afetando outras condições que tornam o evento mais provável, por exemplo, condições atmosféricas e/ou operacionais.
- Causa Raiz
Da literatura de confiabilidade, pode-se resumir que Causa Raiz é: o gatilho de todo o processo de falha.
A IEEE std 500-1984, estabelece que é: a circunstância que induz ou ativa o processo de falha, ou seja, ativa o mecanismo de falha.
Para a ISO 14224-2016, é: o conjunto de circunstâncias que levam a falha.
Todos os conceitos anteriores estão alinhados.
A Causa Raiz é o objetivo dos métodos de Análise de Falha, pois sendo identificada, se pode eliminá-la (quanto possível) para que não se torne recorrente, ou mitigar os seus efeitos.
É a causa mais básica para a ocorrência de uma falha. Vai muito além das causas físicas e operacionais e pode chegar a causas sistémicas, de gestão, ou seja, organizacionais.
- Causa Oculta
A ISO 14224-2016 estabelece Causa Oculta como sendo: aquela que não é imediatamente evidente (identificável) por operadores e mantenedores.
Se enquadram nesse tipo de falha, aquelas que já ocorreram há algum tempo, mas só são observadas sob demanda, ou seja, quando determinada função é ativada ou testada.
Os sistemas de segurança, como bombas de incêndio, geradores de emergência, sistemas de iluminação de emergência, etc., são testados periodicamente para verificar suas funções e se existem esse tipo de falha.
- Mecanismo de Falha
Ainda conforme a ABNT NBR 5462-1994, Mecanismo de Falha é: o conjunto de processos físicos, químicos ou outros que conduzem a uma falha.
Semelhante a ABNT, a IEEE std 500-1984, estabelece que é: o processo físico, químico ou outro processo que resulta em falha.
Na mesma minha, a ISO 14224-2016 define Mecanismo de Falha, como sendo: o processo que leva a falha.
Os processos de falha podem ser físico (elétrico, mecânico, etc.), químico, lógico ou uma combinação desses.
- Efeito ou Consequência da Falha
A ISO 14224-2016 trata Impacto de Falha como: o efeito de uma falha na função ou funções de um equipamento ou da planta.
- Detecção da Falha
É o método ou meio utilizado para a detecção/identificação de uma falha, como por exemplo:
– Inspeção sensitiva (que usa os sentidos humanos);
– Inspeção instrumentada (através de tecnologias como: termografia, análise de vibração, ultrassom, boroscópica, etc.);
– Inspeção detalhada (com desmontagem do equipamento durante a manutenção);
– Monitoramento on-line ou off-line;
– Testes e ensaios (físicos, químicos, lógicos, etc.);
– Teste operacionais.
- Classificação das Falhas Quanto a Severidade
Existem diferenças de classificação das falhas quanto a severidade entre normas, no caso da ABNT e internacionais como IEEE e ISO, portanto fazemos uma comparação na tabela abaixo.
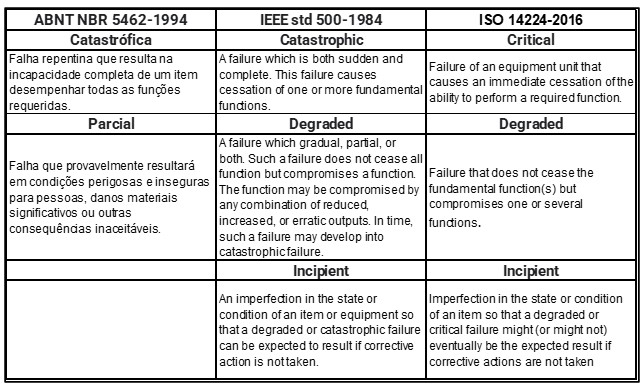
- Análise de falhas
Conforme a ABNT NBR 5462-1994, consiste: no exame lógico e sistemático de um item que falhou, para identificar e analisar o mecanismo, a causa e as consequências da falha. Para detalhes sobre esse tema, veja o artigo http://elektreng.com.br/analise-de-falhas/.
Análise de falha é um tema bastante vasto e importante, então além do artigo mencionado acima que aborda alguns aspectos, deve ser assunto para outras postagens.
Nesse sentido, invocamos Albert Einstein, que disse: “If I had an hour to solve a problem I´d spend 55 minutes thinking about the problem and 5 minutes thinking about solutions“.