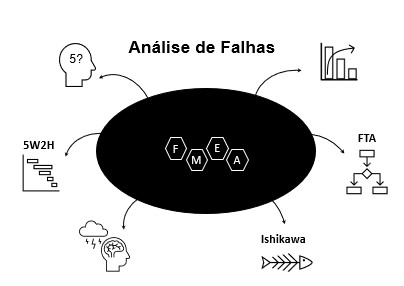
A FMEA – Failure Modes, Effects Analysis (Análise de Modos de Falha e seus Efeitos), foi originalmente desenvolvida na década de 1940 pelas Forças Armadas dos EUA.
Em 1966, a NASA lançou seu procedimento FMECA para uso no programa Apollo. Posteriormente, esse procedimento foi adotado em diversos outros programas aeroespaciais da NASA.
Essa ferramenta inicialmente se destinava às análises de falhas de sistemas e equipamentos do exército americano, após ser aprimorada pela NASA, se tornou usual também nos setores aeronáuticos.
Desde a década de 70 vem sendo usada por vários segmentos como, automotivo, nuclear, industrias de óleo & gás, entre outras, e atualmente sua utilização é mais abrangente e tem aplicação em variados campos da atividade econômica.
A FMEA é uma metodologia analítica e sistemática que objetiva avaliar um equipamento, um item ou um processo, e então identificar as formas como podem falhar, os efeitos do modo de falha no seu desempenho, nas pessoas e no meio ambiente e o que levou a ocorrência da falha.
Existem vários tipos de FMEA, de acordo com a sua aplicação, dentre eles destacam-se:
- FMEA de Projeto – usada para avaliar as suas vulnerabilidades e corrigi-las ou mitigá-las ainda nessa fase, ou seja, antes da implantação;
- FMEA de Fabricação/Operação – é utilizada para identificar as possíveis falhas de um produto, desde a sua fase de produção até a entrega ao cliente;
- FMEA de Processos – aplicada em várias áreas de uma empresa a fim de descobrir pontos de melhoria dos processos com consequências internas ou externas;
- FMEA de Software – destinada para encontrar possíveis falhas nas aplicações tecnológica, aplicativos ou sistemas mais complexos;
- FMEA de Manutenção – amplamente aplicada na elaboração de Planos de Manutenção de forma a que os recursos sejam aplicados corretamente visando a Confiabilidade e Disponibilidade dos ativos.
Esse artigo dará ênfase a FMEA de Manutenção, contudo os passos aqui descritos podem ser usados de forma geral em outras aplicações.
Etapas para Elaboração de FMEA de Manutenção
1 – Definir o Equipamento ou Sistema
Geralmente essa escolha se dá em função da importância do Equipamento ou Sistema (criticidade) ou também devido a incidência de falhas registradas.
É fundamental estabelecer claramente as funções do Equipamento ou Sistema e os limites da análise, que tem correlação com os limites físicos do Equipamento ou Sistema.
2 – Definir a Equipe
A equipe deve ser multidisciplinar, com 6 a 8 componentes, onde um deles será o Coordenador.
O Coordenador ou Líder será responsável pelo planejamento da análise, estabelecendo frequência das reuniões, prazo, meio de registro e controle de todo o processo durante o desenvolvimento da FMEA.
A equipe deve ser composta por profissionais com conhecimento do Equipamento ou Sistema, como também da metodologia, ou que seja feito um nivelamento antes do início do processo.
Geralmente os componentes são das áreas de Operação, Engenharia, Manutenção, Segurança ou de Processo, a depender da situação pode ter um Consultor Externo para contribuir com conhecimento da ferramenta ou da tecnologia do Equipamento ou Sistema em análise.
3 – Análise de Falha
3.1 – Definir os Modos de Falha
Nessa etapa deve-se subdividir o Equipamento ou Sistema em componente ou subsistemas, de forma a que seja identificado como cada um deles falham.
O histórico de falhas é um recurso importante a ser utilizado e na falta dele, pode-se usar dados da literatura técnica ou da documentação do fabricante.
3.2 – Identificar os Efeitos
Para cada Modo de Falha devem ser listadas as consequências, sejam elas para pessoas, para o processo ou para o meio ambiente.
3.3 – Identificar as Causas
Aqui a contribuição dos especialistas é de grande importância para identificação da Causa da Falha para cada um dos Modos de Falha elencados.
4 – Priorizar as Falhas
Nessa fase a avaliação do risco é feita através da quantificação do risco, com base em três vetores:
- Ocorrência – frequência com que a falha ocorre;
- Severidade – impacto em custos, segurança ou produção, caso a falha ocorra;
- Detecção – probabilidade da falha ser detectada;
Para cada um desses vetores deve ser dada uma nota (1 a 10), onde 1 tem pouca importância (baixa frequência, baixo impacto e fácil detecção), e 10 demonstra alta relevância (alta frequência, grande impacto e difícil detecção).
Existem na literatura técnica e normas, tabelas com gradação dessas notas para cada vetor, que facilitam a aplicação na elaboração da FMEA.
O produto desses três fatores compõe o RPN – Risk Priority Number (Número de Prioridade de Risco), que quanto maior for seu valor, maior será a prioridade.
5 – Definir Ações
O RPN será um orientador para definição das intervenções de manutenção, alocando recursos humanos, financeiros e tecnológicos nos itens com maior prioridade, estabelecendo assim a otimização dos recursos.
É possível que após uma FMEA, se chegue à conclusão pela modernização (retrofit ou revamp) ou substituição de parte ou total do Equipamento ou Sistema, mas em geral ações de engenharia são suficientes.
A literatura apresenta vários modelos de formulários de FMEA e existem inúmeros software dedicados no mercado, mas uma planilha eletrônica é o suficiente para se fazer uma boa análise. Para tanto ela deve conter:
- Identificação – onde são registrados as informações do Equipamento ou Sistema (TAG, descrição, função, planta, área, etc.), membros da equipe e Coordenador, data de início e fim da análise;
- Item/Componente/Função – colunas onde serão registrados os componentes que serão avaliados;
- Análise de Falha – colunas onde são descritos os Modos de Falha, os Efeitos e as Causas;
- Priorização das Falhas – colunas onde serão dadas as notas para Ocorrência, Severidade e Detecção e será feito o cálculo do RPN;
- Ações – espaço onde serão elencadas, em função do valor do RPN, as ações preventivas e/ou mitigadoras de risco.
A figura a seguir é um exemplo ilustrativo de um formulário de FMEA de Manutenção, mas pode ser modificado em função da aplicação.

Os registros das reuniões de FMEA (quem participou, quais as premissas e decisões tomadas, etc.) são muito importantes para a elaboração final do documento, para a rastreabilidade, para a tomada de decisões, além de servir de base para futuras revisões em função dos resultados dos Planos de Manutenção.
Benefícios da FMEA de Manutenção
São muitos os benefícios decorrentes da adoção da ferramenta FMEA de Manutenção, mas se destacam:
Identificação Proativa das Falhas
A aplicação dessa ferramenta permite a identificação precoce dos processos de falhas e foco nas atividades de manutenção evitando paradas não programadas e risco para as instalações e seus usuários.
Redução dos Custos
Com a elaboração dos Planos de Manutenção através da FMEA, esses passam a ser menos empíricos ou apenas baseados nas recomendações conservadoras dos fabricantes, com consequente diminuição de intervenções de manutenção e impactos nos custos de mão-de-obra, materiais e contratação de serviços, além de redução de interrupção da produção.
Impacto na Confiabilidade e Disponibilidade
Aplicando e acompanhando as recomendações obtidas na FMEA, a confiabilidade e disponibilidade dos ativos tendem a aumentar e consequentemente a segurança para os usuários, para a integridade dos sistemas e para o negócio.
Suporte na Tomada de Decisões
Como já comentado anteriormente, a FMEA fornece informações valiosas para a tomada de decisões em relação a elaboração dos Planos de Manutenção e de investimentos, influenciando na alocação eficiente de recursos, no planejamento estratégico da manutenção e na definição de medidas preventivas para garantir a qualidade e a excelência operacional.