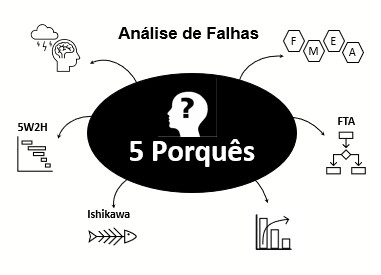
Em Agosto de 2020 postamos um artigo sobre Análise de Falhas, que pode ser acessado no link http://elektreng.com.br/analise-de-falhas/.
Nesse artigo discutia-se que ferramentas usar para realizar uma Análise de Falhas de equipamentos, então afirmava-se que existe uma gama de Métodos de Análise e Solução de Problemas (MASP), mas a recomendação era que adotasse um desses métodos e sistematizasse a sua aplicação.
Claro que quanto mais complexo seja o equipamento, mais elaborado deve ser o processo de Análise de Falha e as ferramentas a serem utilizadas. Mas via de regra, ferramentas simples como Brainstorming, Ishikawa, 5 Porquês, etc., são o bastante para encontrar a causa raiz da maioria das falhas de equipamentos industriais.
Assim, elegemos o Método dos 5 Porquês, para tratarmos nessa postagem, pois mesmo que seja um método simples, pode ser aplicado com excelentes resultados na rotina da manutenção industrial.
Esse método foi desenvolvida na da Toyota na década de 70, com o objetivo de solucionar problemas nos processos produtivos da sua fábrica.
É umas das ferramentas da qualidade e de MASP e aplica-se na análise de falha de equipamentos, investigação de incidentes ou acidentes e/ou em análise de processos ou negócios.
Essa ferramenta busca identificar a causa raiz de um problema, de forma bastante simples. Deve-se realizar várias iterações perguntando o “porquê” daquele problema, sempre questionando a causa anterior. Repete-se o questionamento até atingir o nível raiz, quando não é mais possível desdobrar as causas, então, identifica-se a causa raiz do problema. Geralmente isso ocorre até o quinto porquê, daí o nome 5 Porquês, mas pode ser necessário perguntar mais do que cinco vezes ou, até mesmo parar antes de atingir o quinto porquê.
Após a identificação da causa raiz, elabora-se um Plano de Ação para eliminá-la ou mitigar seus efeitos. O Plano de Ação deve ser acompanhado e verificado periodicamente, para avaliar se as ações foram realmente eficazes.
O fluxo a seguir, ilustra o esse método de Análise de Falhas descrito acima.
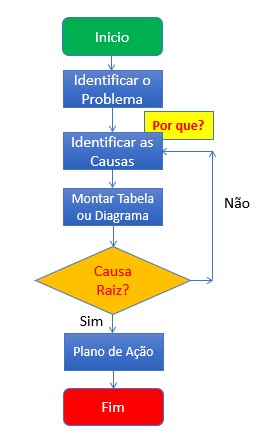
Na aplicação pela manutenção para Análise de Falhas de equipamentos, recomenda-se realizar a reunião de análise o mais breve possível após o evento e a coleta de dados.
É imprescindível formar um grupo multidisciplinar com profissionais que conheçam o equipamento, o processo e as condições operacionais envolvidas e eleger um facilitador ou coordenador, que será responsável por conduzir a análise e registrar todo o processo.
Inicia-se a análise descrevendo de forma clara e concisa a falha (o problema). Em seguida faz-se a primeira pergunta, dando oportunidade a cada participante opinar livremente até que a equipe conclua, por uma resposta válida a questão formulada.
As respostas devem ser baseadas em dados, documentos, observações e fatos, nunca em suposições ou pré-julgamentos, assim muito mais confiável será o resultado da análise. Repete-se essa prática até identificar a causa raiz.
EXEMPLO
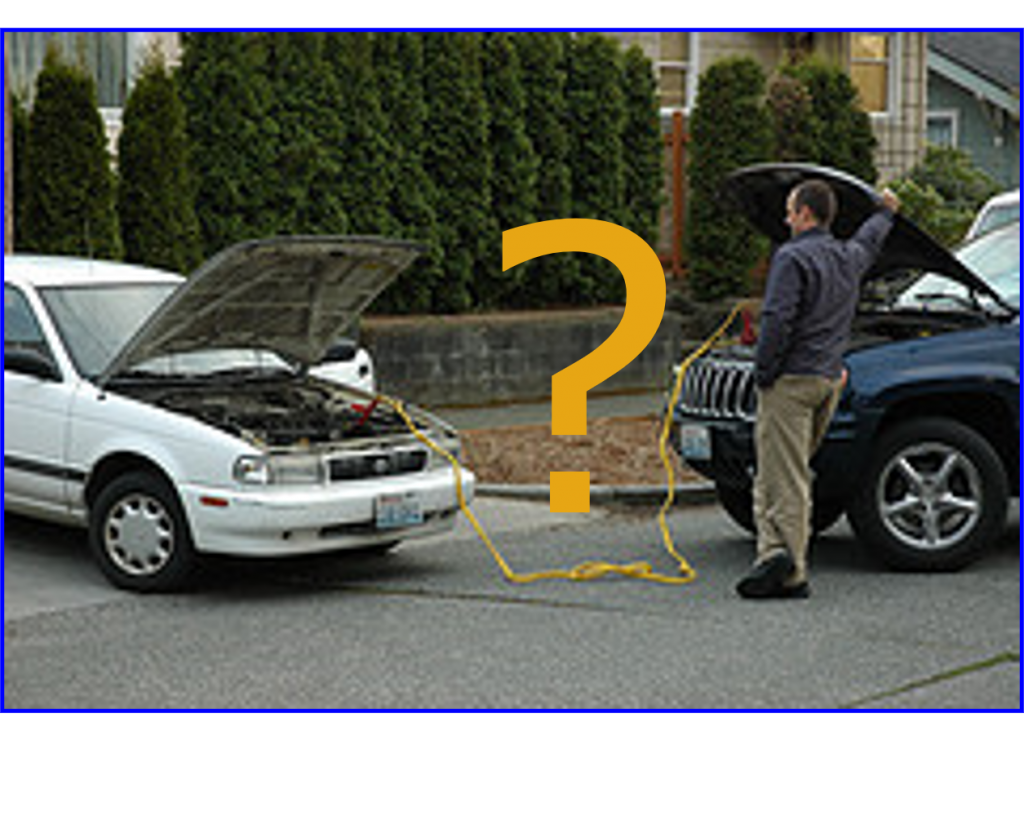
Essa é uma situação que muitos usuários de automóveis já devem ter vivido, ou seja, O Carro não liga, não dá partida quando acionado.
O diagrama a seguir, resume o que poderia ser uma causa raiz para o problema de o carro não ligar, sabendo-se que outras causas poderiam incorrer no mesmo problema.
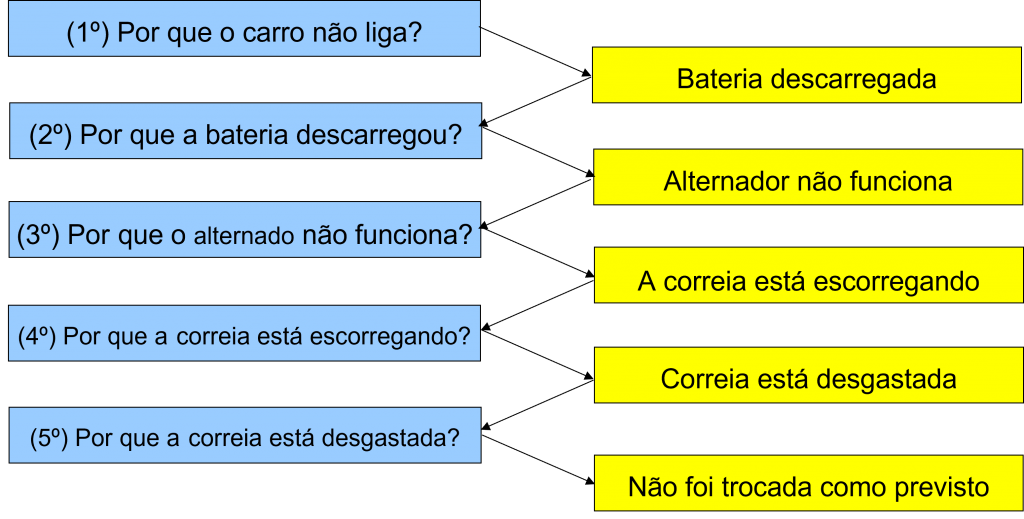
O manual do veículo previa a inspeção periódica da correia de transmissão que aciona o alternador, como também a sua substituição compulsória após determinada quilometragem ou tempo de instalada, o que ocorresse primeiro.
Do exposto anteriormente pode-se concluir que a causa raiz foi o Não Cumprimento do Plano de Manutenção do veículo, definido pelo fabricante.
Por outro lado, a ação recomendada é instruir o proprietário do automóvel a consultar regularmente o manual e fazer as inspeções periódicas e substituição de componentes, ali definidas.