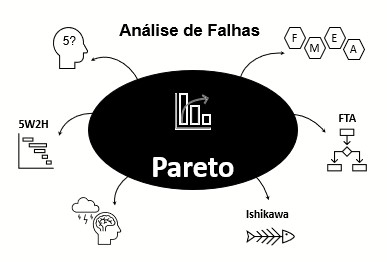
O Método de Pareto, também conhecido como Princípio 20/80 ou Análise de Pareto, foi desenvolvido no século XIX pelo economista e sociólogo italiano Vilfredo Pareto, que ao analisar a sociedade observou que a grande maioria das riquezas estava nas mãos de poucas pessoas.
Posteriormente, Joseph Juran, um dos gurus da qualidade, verificou que este mesmo princípio era válido para tratamento e solução de problemas, ou seja, atacando-se pequena parte das causas (geralmente cerca de 20%) soluciona-se a maioria dos problemas das organizações (por volta de 80%).
Assim, esse método é amplamente utilizado em várias áreas, incluindo gestão de qualidade, resolução de problemas, marketing e análise de falhas de equipamentos industriais.
Esta ferramenta tem sua aplicação recomendada para identificação de fatores que mais influenciam no resultado de um processo ou na busca das causas de um problema, apontando para a priorização de ações de melhoria.
Uma vez realizada à coleta de dados e organizados os dados através da Folha de Verificação, por exemplo, pode-se construir o Gráfico de Pareto, seguindo o roteiro abaixo:
- Identificar o problema ou resultado e suas categorias (áreas, períodos, causas, etc.);
- Quantificar cada uma das categorias;
- Listar as categorias em ordem decrescente de valor;
- Calcular a frequência relativa (frequência da categoria dividida pela frequência total) e a frequência acumulada;
- Construir um gráfico duplo, tipo barras para a frequência relativa e tipo linha para a frequência acumulada (o MS Excel ® tem essa funcionalidade).
Análise de Pareto – Exemplo
A coleta de dados de falha dos equipamentos de uma planta industrial, em um dado período tempo, resultou na tabela a seguir.
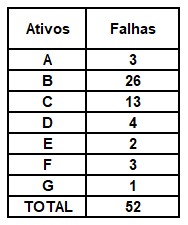
Aplicando-se a Técnica de Pareto tem-se.
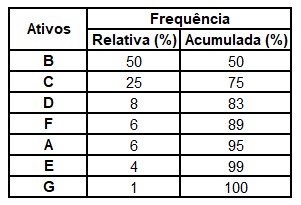
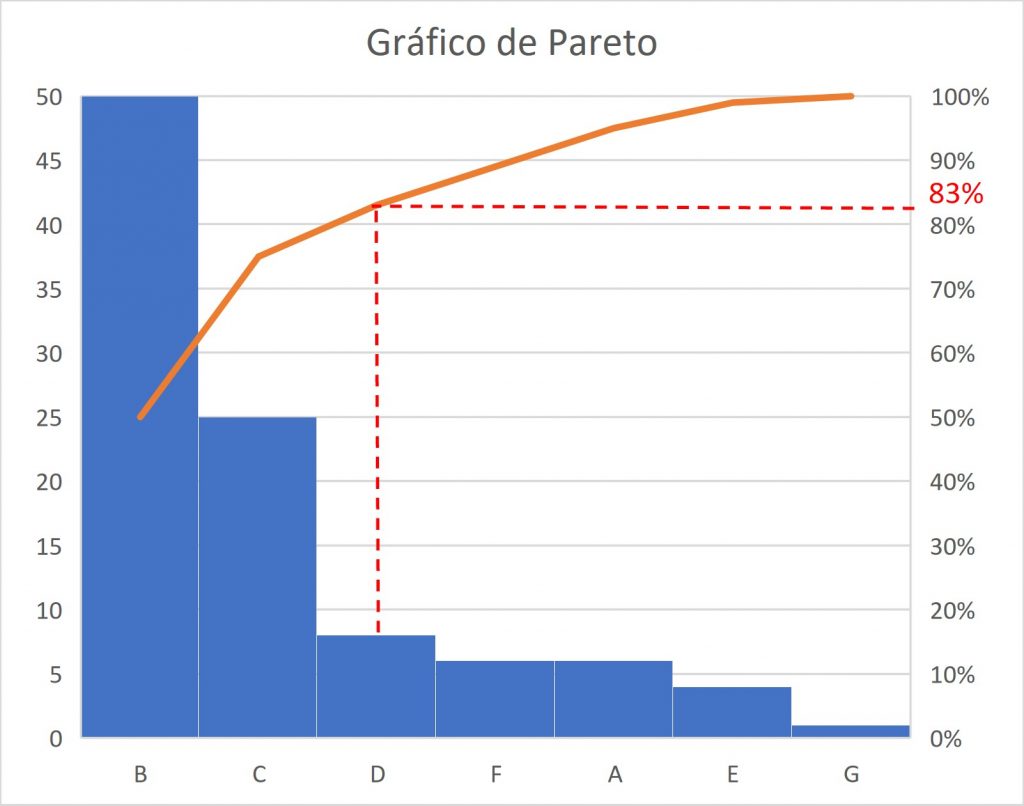
Exemplo de Pareto
Observar-se que os equipamentos “B”, “C” e “D” são responsáveis por 83% das falhas da planta, ou seja, eles representam os Bad Actors da unidade industrial, como são assim chamados no jargão da confiabilidade.
Então, se essas falhas relativas aos Bad Actors, forem analisadas, estudadas, as devidas ações implantadas e acompanhadas, atinge-se um outro patamar de eficiência da planta.
Um outro resultado importante derivado da Técnica de Pareto é a estratificação, onde os mesmos dados são tratados usando-se esta ferramenta sob a influência de diversas causas ou fatores causais, como: custo de manutenção, perdas de produção, área da planta onde ocorreram as falhas, etc.. Os resultados poderiam indicar vários caminhos para tomadas de decisões.
Os dados de falha, conforme já comentado anteriormente, escondem informações valiosas que podem ser reveladas com a Metodologia de Pareto, auxiliando as equipes de engenharia, manutenção e operação, na incorporação de outros métodos de manutenção, desenvolvimento de melhoria nos equipamentos e/ou das condições operacionais e dos ambientes de processo.
A aplicação do Método de Pareto na análise de falhas de equipamentos industriais oferece várias vantagens:
- Problemas Principais: Permite identificar as principais causas de falhas, priorizando a resolução dos problemas mais críticos, o que economiza tempo e recursos;
- Melhoria da Eficiência: Ao abordar as causas principais, a eficiência da manutenção aumenta, reduzindo o tempo de indisponibilidade não planejada dos equipamentos;
- Tomada de Decisão: Fornece uma base sólida para a tomada de decisões, pois os dados são usados para determinar onde a atenção e os recursos devem ser direcionados;
- Monitoramento: O Método de Pareto pode ser usado regularmente para acompanhar a eficácia das ações corretivas e ajustar as estratégias conforme necessário.
Em resumo, o Método de Pareto é uma ferramenta valiosa para identificar e resolver problemas de forma eficiente, priorizando as causas principais. Quando aplicado à análise de falhas de equipamentos industriais, ele ajuda a manter a produção em funcionamento de maneira mais confiável e econômica.